蓄电池极板制造工艺的革新与环保升级
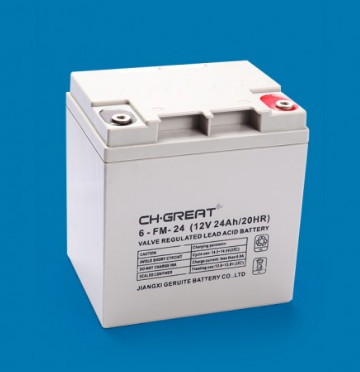
一、传统极板制造工艺的痛点与局限
铅酸蓄电池的核心部件极板制造工艺长期依赖传统重力浇铸技术。该工艺需将铅合金加热至450-550℃高温熔融后注入模具,涉及铅粉制造、板栅锻造、极板化成等关键工序。典型流程包含:
铅粉制备:采用岛津法将电解铅加工成含氧化铅60-80%的铅粉
板栅铸造:使用铅锑/铅钙合金在熔铅炉中高温浇铸成网格载体
极板涂填:将铅膏与稀硫酸混合后涂覆于板栅表面
固化干燥:通过表面干燥和隧道式固化系统形成稳定结构
传统工艺存在明显缺陷:能耗高达800-1200kWh/吨铅,生产过程中产生铅烟、铅渣等污染物,作业环境铅浓度超标50-100倍。更严重的是,重力浇铸形成的板栅存在厚度不均(±0.2mm)、孔隙率波动大(35-50%)等问题,直接影响电池循环寿命。
二、扩网式极板制造的技术突破
针对传统工艺的缺陷,我国研发的连续扩展生产工艺实现三大创新突破:
连轧连铸技术革新
采用铅带连续轧制设备(线速度15-20m/min),将铅液直接铸造成厚度0.6-1.2mm的连续铅带,相较传统浇铸节能40%。通过9工位联动系统完成:
熔铅炉(400±5℃)→保温炉(380±3℃)精准控温
铅带轧制(厚度公差±0.05mm)
数控拉网机(网格精度±0.1mm)扩展成型
冷加工工艺体系
全过程采用常温加工技术,彻底消除铅烟产生。关键技术指标:
网格扩展率300-400%
板栅抗拉强度≥15MPa
厚度均匀性CV值<3%
智能化制造系统
集成视觉检测(精度0.02mm)、自动涂膏(涂布量偏差±1g)、激光切片等模块,实现极板制造合格率从92%提升至99.5%。
三、环保效益与产业升级
新型扩网工艺被列入《国家重点节能技术推广目录》,其环保效益显著:
能耗降低:单位产品能耗从1.2吨标煤/万片降至0.45吨
污染控制:铅尘排放浓度<0.5mg/m³(国标1.0mg/m³)
生产效率:单线产能达6000片/小时,较传统工艺提升5倍
国产化设备价格仅300-400万元(进口设备1000万元以上),已在国内18家企业应用,带动行业改造升级。据测算,全面推广后每年可减少铅排放1200吨,降低职业病发生率80%以上。
极板制造工艺的革新不仅破解了铅酸蓄电池行业的环保困局,更通过装备国产化打破了国外技术垄断。随着连续扩展技术的深度应用,我国正从铅酸蓄电池制造大国向技术强国跨越,为全球绿色能源存储提供中国方案。